Control room acoustics
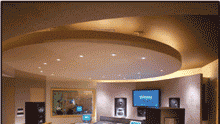
The audio production control room at WNET, New York.
If there is one trend that the professional audio industry recognizes, it is the arrival of fully integrated digital-based broadcast and production facilities. Broadcast-industry control rooms (i.e., those used in radio, television, audio post production, etc.) are, of course, no exception. Much conversation continues over workstation wars, format battles, etc. But, almost everyone agrees on the basic premise that broadcasters need to listen to audio in acoustically accurate environments. In fact, the standards for such environments have been better defined during recent years and address newer issues such as surround sound. In this article, we visit the criteria used to design such environments.
Acoustical criteria
We can think of any critical listening environment in terms of two primary categories of acoustical requirements: sound-transfer acoustics and internal room acoustics. Of course, finished design solutions often integrate both of these categories, but let’s look at them separately to understand them more thoroughly.
Figure 1. This drawing shows variations in floor, wall and ceiling systems for typical isolation sytems, including the difference between ceiling hanger and lid systems.
Sound-transfer acoustics
Production environments need to be quiet. But they often generate quite a bit of noise themselves and disturb surrounding spaces (including adjacent suites). Sound-transfer acoustic design deals with these issues. The goal is to create quiet spaces with typical noise-criteria (NC) values of 15 to 25. A noise-criteria value is a single number that actually represents an algorithm of eight values of octave-band quietness measurements, weighted to reflect human hearing more accurately. The lower the NC value, the quieter the room. Rooms with open microphones typically require an NC value of 15. An NC value between 20 and 25 is acceptable in post-production environments. Knowing the requirement is one thing; achieving it is quite another. Typically, acoustical engineers and architects design the boundaries of the room “container” (the floor, walls and ceiling) to deliver the required NC value. Naturally, the room’s quietness most often is a function of the surrounding environments and good design of the HVAC system. A quiet space is easier to accomplish in a quiet environment (i.e., one with quiet neighbors). For example, in preliminary design, it would be unwise to place an iso/vocal booth (which requires NC15) next to a large mechanical room. Most studios with microphone rooms have similar sound-isolation concerns because the most bothersome noise is often generated from the control room itself.
The professional video industry's #1 source for news, trends and product and tech information. Sign up below.
Figure 2. This figure shows the complex ductwork required for the audio production control room at WNET in New York.
Mainstream acoustic-isolation design in the United States typically uses the “room within a room” design method, employing decoupled floors, walls and ceilings. This method takes into account two important principles: mass and decoupling. Mass refers to density of the room’s boundary surfaces (floor, walls and ceiling). Decoupling refers to the process of isolating the boundary surfaces from the surrounding structure.
Decoupling walls is simple to understand and relatively easy to achieve. It involves using separate stud systems and multiple layers of gypsum board (sometimes sandwiched with stiff materials, such as vinyl or soundboard) separated by a small air space, and then repeating the process. But decoupling the floor and ceiling is more complex since, of course, they cannot really “float.” The best isolated floor is one that has separate concrete slabs. This is usually possible in new construction and in slab-on-grade construction. When this is not possible, it is best to use built-up decoupled flooring systems with the inner partition built on top of this flooring. Isolated (decoupled) ceilings come in two primary flavors: lid or suspended construction. A lid system will usually provide better results since the lid simply is not touching the other elements of the room. But lid systems are limited by the width and depth of the room as well as height (since spanning structural members become very deep as the width and length increase).
Figure 3a. This drawing shows the path of the direct sound and the path of the reflected sound as it bounces off a large production console.
Often, the ability to get long ceiling joists onto the site will determine whether you can use the lid isolation system. If you’re designing larger rooms or rooms with more complex ceiling profiles, you need to install a system of isolated hangers. With this system you must pay careful attention to the selection and exact spacing of these hangers so that the loading is evenly and correctly distributed throughout the system. You can achieve the required boundary-surface mass by using multiple layers of gypsum board for the walls and multiple layers of plywood and gypsum board for the floor (see Figure 1).
Two remaining sound-transfer issues we must consider are room penetrations (doors, windows, conduits, etc.) and HVAC layout. It is ironic that we spend so much time and money on complex, stiff, thick, expensive boundary systems only to make a great number of holes in them. How we organize and detail these penetrations usually determines whether we achieve a successful acoustic-isolation system.
Figure 3b. By simply re-positioning the near-field speaker, the reflection goes away, eliminating the interference and its disturbing frequency response.
Sound behaves very much like water in that it can leak through the smallest of openings. Multiple wall systems entail multiple window frames and glass panes that need to be isolated to avoid resonance and sound leakage. Constructing isolated doors requires the same attention to detail. The quietness of a room is often limited by the quietness of its HVAC system. For example, designing a room to have an NC value of 20 (which is quite quiet) would require designing an HVAC system with an NC value of 20 or lower. There are several important components and techniques you can use to minimize HVAC sound transfer:
- Use large ducts to create lower-than-normal airflow speeds;
- Use lined ducts to reduce machine noise traveling down the ducts
- Mount heavy equipment with springs and/or mass dampening pads; or
- Minimize room penetrations as they pass through the sound boundary container.
For example, Figure 2 shows the complex ductwork required for the audio production control room at WNET in New York. Remember, site selection is critical. And keep in mind that political solutions for quietness control are often the best ones. A quiet space is easiest to accomplish when you locate it next to quiet neighbors. Designing a small vocal iso booth to be NC15 at 63Hz may not be the best way to spend your money, since you probably won’t be recording any information at that frequency in such a room. Also, try to avoid lightweight structures. Slab-on-grade sites are usually superior.
Internal room acoustics
Internal room acoustics is the study of how sound is propagated in an enclosed space.
Figure 3c. These graphs show the frequency response at the operator’s listening position for each placement of the speaker.
Small-room acoustics in stiff boundaries (these are the spaces we are typically dealing with) concerns several different criteria and issues. We can control internal room acoustic behavior by controlling room size and shape as well as surface treatments. Think of a small room as two separate rooms that behave differently at higher and lower frequencies. At mid and high frequencies (above 200Hz), we can treat sound a bit like rays of light, which travel in straight lines. At these frequencies, a room’s reflection patterns can affect sound perception at a critical listening position. For example, Figure 3a shows two paths taken by sound emanating from a near-field speaker mounted on a production console. One is a direct path to the console operator; the other is an indirect path reflected off the console. The reflected sound arrives at the operator’s listening position just a few milliseconds later than the direct sound, and at a dB level not that much lower than the direct sound. The two sounds interfere with one another, and the result is a disturbing frequency response for the operator.
Figure 3b shows that, by simply re-positioning the near-field speaker, the reflection goes away, eliminating the interference and its disturbing frequency response. Figure 3c shows the frequency response at the operator’s listening position for each placement of the speaker. Notice that when the speaker is placed on top of the console, the frequency response at the operator’s position (shown in the top graph of Figure 3c) is similar to that created by a comb filter. Figure 3d shows how to calculate the frequency of the first null created by this comb-filter effect.
At lower frequencies, however, sound is less directional and thus reflection control becomes less relevant. At these frequencies, the ratio of raw room dimensions and the position of speakers and listener are more significant. The overall dimensions of the room will effect the natural distribution of eigentones (standing waves).
Figure 3d. This figure shows how to calculate the frequency of the first null created by the comb-filter effect.
Since the rooms that we are dealing with typically have stiff boundaries because of their sound-isolation requirements, there is little chance for the low frequencies to be absorbed. The surface treatments that we most commonly associate with audio rooms (i.e., acoustic foam, acoustic panels, etc.) are relatively thin. They can convert mid- and high-frequency sounds to heat, but they have little effect on lower frequencies, which simply arrive at the stiff boundaries and reflect back into the room.
A common misconception is that standing waves are bad. Standing waves always exist in a closed environment. What we strive to do is to space these frequencies as evenly as possible. Think of standing waves as an indication of a room’s ability to resonate – to “ring out” or reinforce tones naturally. You can imagine that if the proportions of a room are chosen correctly, then there will be a more natural spacing of the tones and the room will tend to reinforce lower-frequency tones more evenly. This is a good thing. The opposite, of course, would be harmful and tend to cause uneven frequency response at a critical listening position – not a good thing for audio playback.
Figure 4a. This drawing shows a 20-foot by 20-foot room plan and its modal distribution.
So, the first step in room acoustic design (after making sure that all equipment and furniture fits) is program satisfaction. Try to choose a room shape that will space (organize) the low-frequency eigentones as evenly as possible.
By the numbers
A story about room design and standing waves comes to mind. I received a phone call one day from a student with what he thought was a simple question. He said, “I have a 20-foot by 20-foot room that I want to use as a control room for my new studio. What should I do to make it sound good?” That’s a big question. Half of me wanted to explain that this was not really a one-sentence (or one-concept) answer, but my other half accepted the challenge of trying to give him a simple answer. After a minute of thinking, I answered, “Build a closet.” He probably thought I was joking, but I still believe this was a realistic answer.
Figure 4b. This drawing shows a 16.5-foot by 20-foot room plan and its modal distribution. Note that as frequency rises, modal packing becomes so dense that eigentone analysis is no longer important. At that point we are more concerned with “ray acoustics,” i.e., reflection control.
The square room (20 feet by 20 feet) is almost the worst possible shape you can have. The only thing worse would be a 20-foot cube. Width and length of identical dimensions will, of course, cause many of the lower-frequency eigentones to be identical, resulting in harsh frequency anomalies – a pileup of energy – as well as voids at other frequencies (see Figure 4a). These frequencies are not that hard to calculate (f = 565/ room dimension). Multiplying this value by 2, 3, 4, etc. gives you the frequencies for that particular dimension. Doing the same for the two other primary dimensions and then listing the frequencies will easily give you this distribution.
By building a closet in the room, he could, for example, create a listening room that was 20 feet wide and (more or less) 15.5 feet deep – a much better room ratio (see Figure 4b). He also would end up with a closet for storage, and possibly a good location for noisy equipment and other devices. Notice that I suggested that 20 feet should be the width of his room. This is because by having the side walls further away from the listening position, you improve mid- and high-frequency reflection control. You can easily analyze room ratios by using a very well-known industry “pictogram” of accepted room ratios, first published by Newman, Bolt, Beranek in 1957 (see Figure 5). Using the pictogram involves three basic steps:
- Divide all room dimensions by the height (making the height equal to 1).
- Plot width and length on horizontal and vertical scales.
- Determine acceptability by noting whether plot is in or out of the “zone.”
Figure 5. This “pictogram”of acceptable room ratios was first published by Newman, Bolt, Beranek in 1957.
There is no one perfect room ratio. If there were, we would all know it and thus not have to deal with this problem. Also, there are often situations in which architectural restrictions such as columns, height limitations, etc. would thwart your attempts to create a room with well-distributed eigentones. If you can’t create a room with a well-distributed lower-frequency eigentone balance, then you should use carefully placed low-frequency absorption to minimize these buildups. But accomplishing this with thin materials is tricky. You can use membrane absorbers or Helmholtz resonators. You can achieve even better low-frequency absorption efficiency by adding air space behind more typical broadband absorption materials.
Summary
- Remember that site location sometimes can be the most important part of designing a quiet room.
- Try to create a room-plan layout with room ratios (width, length, height) that create acceptable low-frequency eigentone distribution.
- Use geometry and well-applied surface treatments to distribute mid- and high-frequency “rays” to eliminate time anomalies that can create harsh frequency functions.
All this must be accomplished without sacrificing the architectural goals of the room: ergonomics and room layout. We will discuss this aspect in an article next month.
John Storyk is a principal owner of the Walters-Storyk Design Group.