Systems Design Showcase: Acoustics issues for studio design
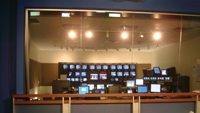
Sound generated by building users and services – in particular, mechanical, electrical and power systems – are key sources of noise intruding upon television studios. Successful design and construction of a quiet, intrusion-free television studio requires close cooperation among the owner, design architect/engineer, acoustical engineer and construction manager from the earliest planning phase through the final construction.
Some facilities build control rooms with acoustic ceilings and wall panels to reduce the impact of production equipment noise.
The purposes of a TV studio and its location within the building have significant effects on acoustical design. A formal studio used for live recording of shows with an audience and/or music is subject to high heat loads generated by studio lighting, as well as the presence of a large number of people. This setting requires high air volumes to achieve adequate cooling.
At the same time, the use of boom microphones requires that the studio have both an NC rating of 25 or lower and the absence of intrusive noise from building services and occupant activity, a particularly acute issue in a multi-tenant commercial building. In fact, this type of studio presents the greatest acoustical challenges.
In contrast, a news/sports/weather studio featuring anchors and reporters using lapel microphones is much less sensitive to intrusive noise. The heat loads generated by studio lighting will require a higher capacity air handling system, but this can usually be met using conventional systems. Likewise, sound separation can be adequately addressed using conventional construction. NC 30-35 is acceptable in this application.
Similarly, a newsroom studio requires less specialized acoustical and air handling equipment than a formal studio. Typically the newsroom studio is designed as a large open office with high ceilings. The additional lighting required for broadcasting does not generally add significantly to the overall heat load. Anchors and reporters wear lapel microphones and are separated from the rest of the newsroom either by a glass partition or open space. Whatever small amount of newsroom sound is audible to viewers (e.g., ringing telephones) actually contributes to the desirable effect of a working local news staff. Since the acoustic and cooling issues are less critical than in a studio for live recording of shows using boom microphones, construction costs also are lower. NC 30-35 (the standard for most offices) is acceptable in this application and generally can be met with a standard office air handling system.
A room within a room
The professional video industry's #1 source for news, trends and product and tech information. Sign up below.
The acoustical requirements of an NC 25 live-audience studio in a multi-tenant building generally are best met using room-within-a-room construction. A floating six-inch concrete floor is supported by springs with a two-inch air space between it and the building slab. The springs provide vibration isolation, preventing transmission of sound from the building slab, while the air space increases airborne sound transmission loss. The studio’s walls are built on top of this floating slab and attached to its ceiling, which is suspended from the building slab above by sound isolation hangers.
High ceilings and absorptive finishes can be used to create a quiet, comfortable working environment in facility newsrooms.
Specialty doors with acoustical values similar to the double walls must be installed to accommodate people and sets. These double doors, often up to 10 feet high and eight feet wide, are very heavy, requiring special goalpost framing made of structural steel tubes with isolated male/female restraints at the top of the structure. Specialty products are manufactured for floating floors, acoustic doors, acoustic windows, floating wall restraints and supports, enabling construction without field-built items. Use of prefabricated materials enables better quality control and reduces errors while speeding construction.
Similarly, drywall construction is preferable to concrete block construction for ease and cost of construction, as well as acoustical control. In fact, several layers of drywall with air spaces between yields better acoustical control with far less weight than masonry construction.
Often the most sensitive room is the voice-over room, which must be very quiet (i.e., NC 15-20) and free of intrusive nose. Typically, these are designed as floating rooms measuring six feet by six feet, with all surfaces finished with sound-absorbing material to create a “dead room” that avoids coloration of voice.
For the formal NC 25 studio, the ideal is a box that is free from contact with the base building except through acoustical elements. The need to run utilities (air supply and returns, cables, etc.) into the room compromises this ideal, requiring additional acoustical controls. This is particularly true of the air handling system, which needs large sheet metal ducts for supply and return air.
Meeting the NC 25 requirement of a formal TV studio usually requires an air handling system dedicated to that studio, a separate system dedicated to serve areas such as technical areas, audio and video control rooms, editing rooms, and master control rooms. And another system is needed to serve the offices. This enables the systems to be run at full capacity only as needed, saving money on operation.
Good noise control starts with effective design at the core of the system. Low-frequency noise can be a problem in contemporary buildings, which utilize variable air volume systems and smaller floor fan rooms. Because noise is generated by sound radiating from HVAC equipment, proper selection and positioning of this equipment in machine rooms is essential for effective noise control. Careful orientation of the fan units with respect to the main supply ducts optimizes acoustic conditions.
Stations can fulfill the NC 25 requirement of a TV studio by using glass to separate the studio from newsrooms and other technical areas.
Theoretically, equipment in a machine room can be positioned in any configuration and supply ducts can run in several different ways. In practice, however, machine rooms and plenum space have shrunk in size as rental space has become more valuable, placing constraints on the installation. Still, optimal positioning and cost-effective source noise control can be achieved. Careful orchestration of the mechanical system with the architectural design is essential to achieving acoustic goals.
Noise also can be controlled downstream of the air handling units through various duct acoustic treatments, most commonly, duct lining or duct sound attenuators. Duct lining and duct sound attenuators are a series of baffles constructed using perforated metal and a fill of fiberglass. Each sound attenuator carries a pressure drop penalty that varies based on performance and air velocity. A three- to five-foot silencer can be incorporated in lieu of lining the entire section downstream of the fan-powered and variable air volume (VAV) boxes.
Treating the exterior of the duct is an additional tool to further reduce radiated noise. One solution uses heavier gauge metal for the ducts themselves, another requires attachment of an exterior soffit with a sandwich of insulation between it and the duct or a drywall casing directly attached to the duct. The exterior soffit costs more and uses more space than drywall, but it affords better noise control. Each of these methods is effective; the choice involves trade-offs between noise control, cost and space.
Efficient system design will minimize the need for noise control. This involves fan/air handling unit selection for low noise rather than low cost and careful location of the unit to maximize duct lengths. For example, variable speed drives (VSDs) are now used to control air volume since they reduce noise and energy consumption at part load conditions. Older systems of control, such as variable inlet vanes (VIV), actually increase noise generation and provide no energy savings for part load conditions.
Air velocities must be kept as low as possible or the system will generate unacceptable noise levels, yet velocities of 400 to 500 feet per minute are common at diffusers. Generating high air volume at low velocity requires use of large air ducts, which need a lot of space. Again, early planning is crucial to ensure that studio height will accommodate air supply ducts and diffusers, which usually are right above the lights.
Conventional air diffusers cannot properly diffuse air at these lower volumes. To avoid air “dumping” and cold spots, site-constructed “plaques” — flat plates with sound-absorptive material on top –- can be installed under the supply duct openings to stop dumping.
Common mistakes
There are a number of common mistakes in designing and constructing broadcast facilities. Mechanical, electrical and plumbing (MEP) equipment are located adjacent to studios without careful thought to noise control. MEP services are frequently allocated inadequate space, making noise more prominent and leading to nosier conditions in directly adjacent spaces. Or a dining room is located near the studio, but without properly treating it for acoustical control of impact noise.
The heavy concentration of computers in TV equipment rooms creates an additional source of noise from the large volume of HVAC equipment required to cool it, yet for operational reasons these are sometimes located close to control rooms and studios rather than separated, perhaps, by a video control room. Corridors around the TV studios are used to carry typical traffic around the facility, and storage rooms are placed nearby, rather than isolating these sources of activity-related intrusive noise.
Lack of effective construction management can defeat an otherwise effective acoustical design. For example, an electrical contractor may lay cable conduit in a straight line, even though it was designed to be run offset in wall cavity space. Another contractor may knock a hole in the wall rather than cutting it, leaving debris in the wall cavity that bridges the sound isolation. Another contractor may adjust the layout of MEP equipment to suit “efficient” or fast installation, adding elbows or shortening ducts, or locating it dangerously close to outlets. The result often is the generation of noise that will be difficult to trace to the source and attenuate.
Early planning and teamwork are keys
The goal of a quiet, intrusion-free television studio can be achieved cost-effectively only through close cooperation between the owner, design architect/engineer, acoustical engineers and construction manager at every step from the earliest planning phase through the completion of construction. Indeed, acoustical engineers should be proactive members of the design team and should be utilized from the planning stages of the project. While acoustical problems can be remedied, it is infinitely more effective when good acoustics are properly designed into a television studio project.
The acoustical engineer’s objective is to work with the architect, designer and/or mechanical engineer from the earliest stages to present design alternatives that ensure precise acoustical performance and acute vibration control. Establishing a baseline as a starting point, the acoustical engineer can help the owner define goals and then work with the architect to apply appropriate solutions for achieving them. This kind of teamwork has a substantial positive effect not only on the acoustical solutions, but also on the bottom line.
Stephen G. Lindsey is a principal with Cerami Associates, a New York City-based acoustics and audiovisual consulting firm.